Ever had your hydraulic machinery throw a fit? It happens! Hydraulic cylinders, the muscle behind many industrial giants, aren’t immune to issues. But fear not! With a little know-how, you can tackle these common hiccups head-on. In this blog post, Renflo Hydraulic Hose Service dives to the nitty-gritty of the most typical hydraulic cylinder problems and walk you through practical solutions. From seal leaks to cylinder drifts, we’ve got you covered. So, let’s roll up our sleeves and get ready to keep those cylinders running smooth as silk!
Seal Leakage
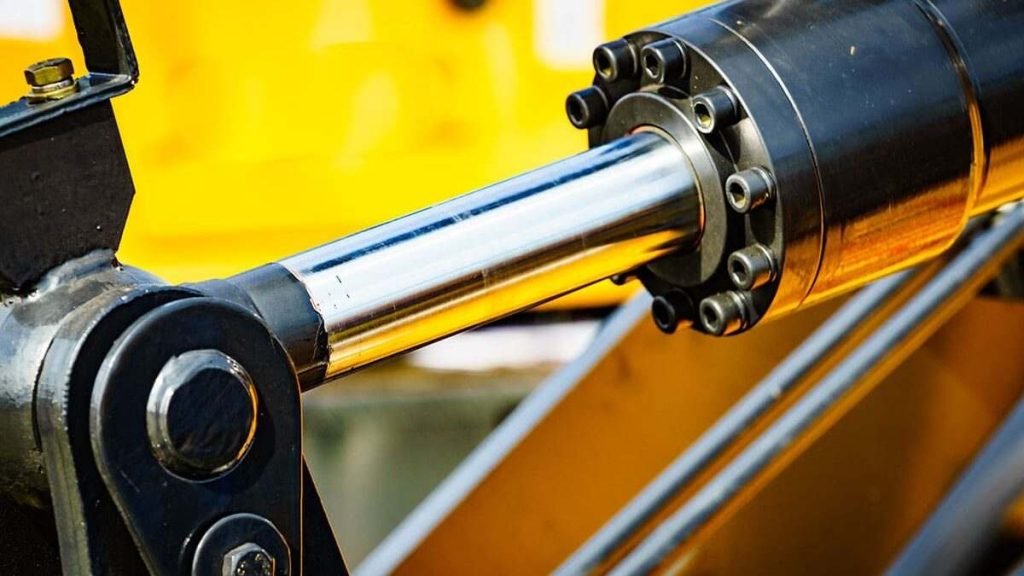
One of the most prevalent problems with hydraulic cylinders is seal leakage. Seals can deteriorate over time due to factors such as wear, high pressure, temperature fluctuations, and contaminants in the hydraulic fluid. When seals fail, hydraulic fluid can leak, leading to reduced efficiency and potential damage to other components.
Seal leakage in hydraulic cylinders is a persistent issue, often caused by wear, high pressure, or contaminants in the hydraulic fluid. When seals deteriorate, hydraulic fluid escapes, leading to decreased efficiency and potential damage to surrounding components. To address seal leakage, proactive maintenance is essential. Regularly inspect seals for signs of wear or damage, and replace them promptly to maintain system integrity. Using high-quality seals and ensuring proper installation can also help prevent seal leakage and extend the lifespan of hydraulic systems.
Solution:
Regular inspection and maintenance are essential for preventing seal leakage. Replace worn or damaged seals promptly to maintain the integrity of the hydraulic system. Additionally, using high-quality seals and ensuring proper installation can help prolong seal life and minimize the risk of leakage.
Bent or Damaged Rod
Hydraulic cylinder rods can become bent or damaged due to overloading, misalignment, or external impact. A bent rod can cause uneven wear on seals, leading to leakage and compromised performance. In severe cases, a bent rod can result in cylinder binding or failure.
A bent or damaged rod in a hydraulic cylinder can severely impact its performance and pose safety risks. Common causes include overloading, misalignment, or external impact. When a rod becomes bent, it can lead to uneven wear on seals, seal leakage, or even cylinder binding, compromising the entire system’s efficiency. Addressing this issue promptly is crucial to prevent further damage and ensure smooth operation.
If you’re facing rod damage in your hydraulic cylinder in Houston, don’t hesitate to seek professional assistance. A reputable hydraulic cylinder repair service in Houston can assess the extent of the damage, accurately diagnose the root cause, and perform the necessary repairs or replacements with precision and expertise. By partnering with a trusted repair service, you can restore your hydraulic system to optimal condition, minimize downtime, and enhance productivity.
Solution:
Inspect rods regularly for signs of damage or bending. If a bent rod is detected, it should be replaced promptly to prevent further damage to the cylinder and other components. Properly aligning equipment and avoiding overloading can help minimize the risk of rod damage.
Rod Seal Failure
Rod seals play a critical role in preventing hydraulic fluid from leaking past the piston rod. When rod seals fail, fluid can escape, leading to decreased efficiency and potential contamination of the surrounding environment.
Rod seal failure in hydraulic cylinders is a common issue that can lead to hydraulic fluid leakage and diminished performance. These seals play a critical role in preventing fluid from escaping past the piston rod. Factors such as wear, improper installation, or contamination can contribute to seal failure. Addressing rod seal failure promptly is essential to prevent further damage to the cylinder and maintain system integrity. By identifying the root cause and replacing damaged seals with high-quality replacements, you can restore the efficiency and reliability of your hydraulic system.
Solution:
To address rod seal failure, its important to identify the root cause, which may include factors such as excessive pressure, improper installation, or contamination. Replace damaged or worn rod seals as soon as possible and ensure that replacement seals are compatible with the operating conditions of the hydraulic system.
Cylinder Drift
Cylinder drift refers to the unintentional movement of the piston when the system is supposed to be at rest. This issue can occur due to internal leakage within the cylinder or valve malfunctions, leading to a loss of positional accuracy and decreased productivity. Cylinder drift, characterized by the unintended movement of the piston when the system should be at rest, is a common issue in hydraulic cylinders. This phenomenon can result from internal leakage within the cylinder or malfunctioning valves.
Cylinder drift not only compromises positional accuracy but also diminishes productivity and efficiency. To address this issue, thorough inspection and troubleshooting are necessary. Identifying and rectifying internal leaks, such as worn seals or damaged components, along with ensuring proper valve operation and adjustment, can effectively mitigate cylinder drift. Timely intervention is crucial to maintaining optimal performance and prolonging the lifespan of hydraulic systems.
Solution:
To address cylinder drift, inspect the cylinder for internal leaks, including worn seals or damaged components. Additionally, check the hydraulic valves for proper operation and adjustment. Regular maintenance and troubleshooting can help identify and resolve issues contributing to cylinder drift.
Fluid Contamination
Contamination of hydraulic fluid is a common issue that can adversely affect the performance and lifespan of hydraulic cylinders. Contaminants such as dirt, debris, water, and air can enter the system through various means, including improper maintenance practices, damaged seals, or external sources.
Fluid contamination poses a significant threat to hydraulic systems, compromising their efficiency and longevity. Contaminants such as dirt, water, and debris can infiltrate the hydraulic fluid through various sources. This contamination can lead to component wear, seal degradation, and impaired system performance. Preventive measures such as employing high-quality filtration systems, maintaining cleanliness during fluid handling, and implementing regular fluid analysis are essential to mitigate fluid contamination. By safeguarding hydraulic fluid integrity, operators can prolong equipment lifespan and ensure reliable operation of hydraulic systems.
Solution:
Preventing fluid contamination requires a combination of proactive measures, including using high-quality filtration systems, maintaining cleanliness during fluid handling and storage, and implementing regular fluid analysis and replacement schedules. Additionally, sealing off hydraulic systems from external contaminants can help minimize the risk of contamination.
Reduced Speed or Force
Over time, hydraulic cylinders may experience a decrease in speed or force output, which can impact productivity and efficiency. This issue can result from factors such as worn components, inadequate fluid levels, or improper system design.
Reduced speed or force output in hydraulic cylinders can result from factors such as worn components or inadequate fluid levels. This issue diminishes system performance and productivity. To address it, thorough inspection and maintenance are crucial. Identify and replace worn components promptly, ensuring proper fluid levels and viscosity. Additionally, consulting with hydraulic specialists to optimize system design and operation can help restore speed and force output to desired levels.
Solution:
To address reduced speed or force, conduct a thorough inspection of the hydraulic system to identify any worn or damaged components. Replace worn seals, rods, or other critical parts as needed. Additionally, ensure that the hydraulic fluid is at the proper level and viscosity for optimal performance. Consider consulting with a hydraulic specialist to assess system design and identify opportunities for improvement.
Overheating
Excessive heat buildup in hydraulic cylinders can occur due to factors such as high operating pressures, inadequate cooling, or prolonged operation under heavy loads. Overheating can lead to fluid degradation, seal failure, and reduced component lifespan. Overheating is a common issue in hydraulic systems, often caused by high operating pressures or inadequate cooling mechanisms. Excessive heat can lead to fluid degradation, seal failure, and reduced component lifespan. To address overheating, ensure the system is properly sized and equipped with adequate cooling measures such as heat exchangers or fans. Monitor operating temperatures regularly and adjust pressure settings as needed. Proactive maintenance and troubleshooting can help prevent overheating and maintain optimal hydraulic system performance.
Solution:
To prevent overheating, ensure that the hydraulic system is properly sized and designed for the application’s requirements. Adequate cooling measures, such as heat exchangers or cooling fans, can help dissipate excess heat. Monitor operating temperatures regularly and address any issues promptly, such as adjusting pressure settings or improving cooling efficiency.
External Damage
Hydraulic cylinders are often exposed to harsh operating environments, increasing the risk of external damage from factors such as impact, abrasion, or corrosion. External damage can compromise the structural integrity of the cylinder and affect performance. External damage to hydraulic cylinders poses a significant risk to their structural integrity and performance. Factors such as impact, abrasion, or corrosion can compromise the cylinder’s functionality, leading to leaks or failure.
Prompt detection and repair of external damage are crucial to prevent further deterioration and ensure safe operation. In Houston, where industrial operations thrive, partnering with a hydraulic hose make-up service can provide comprehensive solutions. These services not only specialize in repairing hydraulic hoses but also offer expertise in addressing external damage to hydraulic cylinders. By entrusting your hydraulic system to professionals, you can minimize downtime and maintain operational efficiency.
Solution:
Implementing protective measures such as guards, covers, or shields can help mitigate the risk of external damage to hydraulic cylinders. Additionally, regular inspection and maintenance can help identify and address signs of wear or damage before they escalate into more significant issues.
FAQs
What is the most common failure on hydraulic cylinder?
Seal Leakage: This is one of the most common reasons for cylinder failure. Seal leakage can be caused due to a variety of reasons such as incorrect fitting, inappropriate metalwork clearances, etc. However, marking on the seal grooves, or corrosion are another reasons that may affect the seal.
How do you troubleshoot a hydraulic cylinder?
Look for oil stains or puddles around the cylinder, as well as wet or discolored areas on the surface. Additionally, you should check for damaged seals or piston rods, as these are potential sources of leakage. Another frequently encountered problem is cylinder drift, where the cylinder fails to maintain its position.
What are the 5 main problems in hydraulic system?
The most common causes of poor hydraulic performance are particulate contamination, water contamination, clogged filters, high fluid temperature and incorrect hydraulic fluids.
How do you inspect a hydraulic cylinder?
Check for dirt or foreign materials in the fluid with regularly scheduled samples sent out for analysis. Inspect the filter for any clogs. Inspect the cylinder rod for signs of weakness or stress. A rough, bent, or scored rod will damage seals or allow for leaks.
How to repair hydraulic system?
- Check the fluid level and quality.
- Inspect the hoses and fittings.
- Clean the components and the environment.
- Test the pressure and the flow.
- Adjust the settings and the alignment.
- Follow the maintenance schedule and the manual.
- Here’s what else to consider.
Conclusion
In conclusion, mastering the art of troubleshooting hydraulic cylinder issues is crucial for maintaining smooth operations in various industries. By identifying and addressing common problems such as seal leaks, rod damage, and fluid contamination, you can prolong the lifespan of your hydraulic systems and minimize downtime. Remember, regular inspection, proactive maintenance, and prompt repairs are key to ensuring optimal performance. With the knowledge gained from this guide, you’re well-equipped to tackle any hydraulic cylinder hiccup that comes your way. So, keep those cylinders in top shape, and keep the wheels of industry turning smoothly!